|
So What
Makes A Tank, Special? |
|
A Standard
Tank - T11.
What do we mean by a ‘standard tank’, and what things make
a tank ‘special’? The most common tank type (Portable Tank
Instruction T11) within the Lessors fleets has the following specification:-
a) 4 Bar working pressure and a 6 Bar test
pressure.
b) Minimum shell thickness of 6mm in mild
steel or the equivalent in stainless steel.
c) a bottom discharge valve with a 3”
BSP, plus a provision for top.
d) steam heating.
e) 1 PV
f) Tare weight between 3,750 – 4,200kg.
g) Insulation of 50mm.
h) Design temperature – typically 120°C,
but could be as low as 93°C.
i) Capacities ranging between 17,500 –
26,000 litres.
j) Within ISO.
This tank type will generally carry more variety of products than any
other.
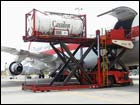
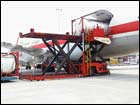
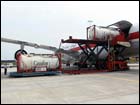
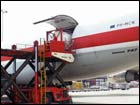
Printing
for best results use the links below to download as PDF
download
page
download
section |
|
1) Maximum
Operating Weights in different parts of the world.
The Maximum Operating Weights can vary from one country to another. Some
states within the USA are more restrictive than many other countries.
Japan used to be about the most restricted, but they are now in line with
European standards. For example, in California the maximum payload for
the tank, the chassis and the cab (including the driver!!) is 80,000 Ibs.
To combat this, the manufacturers have produced lightweight tanks of a
Beam design, where the tare weight is as low as 3,300kg. Of course, rail
can handle higher operating weights.
2) Pressure / Shell Thickness.
The more dangerous the liquid, the higher the pressure rating of the tank
required. The calculation pressure for some substances may exceed the
test pressure of a ‘standard tank’, therefore a thicker shell
would be required - building in more safety of the tank from impact, etc.
and from the product itself. Also the higher the vapour pressure of the
liquid will determine the tank used. To convert from mild steel to stainless
steel, requires the manufacturer to calculate it for you, as he will be
the only person who has the mil certificates stating the values of the
steel used for that tank. Some products, such as bromine (UN No1744) requires
a minimum shell thickness of 12mm in mild steel. Due to the high SG of
3.12, the tank would be made of mild steel, and would require a lead lining.
3) Top
or Bottom Discharge Valve?
Certain high hazardous cargoes are prohibited to load / unload through
the bottom valve, so a valve on the top is required. This then becomes
a so-called "top discharge" tank. It may also be referred to
in the regulations as a tank where no openings "below the level of
the liquid" are allowed. Apart from the bottom outlet, it’ll
probably have all other fittings as described for a ‘standard tank’.
However, a top discharge tank is fitted with a syphon tube (dip pipe /
tube) which is placed inside the tank, usually over a little sump set
into the bottom of the tank shell. The syphon tube will normally be closed
by one outlet valve and a bolted blind flange. Such a tank is fitted with
two or more connections on top of each of which is closed with its own
valve and bolted blind flange for purposes of filling, pressure discharging
and vapour return in order to balance pressure.To move the valve from
the bottom to the top, would cost in the region of US$1,000.00. Any conversion
needs to be certified by a competent authority (BV, DNV, ABS). A Hydrostatic
Test (5 year periodic test) has to be performed. The heat from the welding
up the plate could cause corrosion at a later date.
4) Linings
Linings should be continious of the shell, pipes and valves (through the
welds). i.e. continues to all areas where the product can go.
Most common is rubber. There are many types – butyl, nitrile, natural,
etc. These are closely followed by resinous type linings. Glass flake
is also used. PVDF has been used as a substitute for lead. It all comes
down to compatability.
An alternative to a lining, is a thicker shell, but an allowance for corrosion
is required.
EXAMPLE. Due to the corrosive properties of Hydrofluoric Acid,
the Lessor shall apply a corrosion allowance of 0.2 mm per annum. Any
corrosion above this allowance will be charged at a rate of US$400.00
per 0.1mm per annum.
(continued in next column) ^top^
|
|
4)
Linings (continued)
A wall thickness measurement stating the exact thickness of each
such Container shall be detailed on the on-hire survey. At the end of
the Lease the wall thickness of each such Container shall be measuered
by a competent authority to determine any corrosion during the period
of on hire. The results thereof shall be binding for both parties.
A following graph is a very crude ‘rule of thumb’ indicator
for corrosion versus solution strength. It works for Sulphuric Acid and
Nitrogen, but not for HCL.

The higher the temperature the increase in corrosion.

Purity levels of the product are a factor. The less pure the product is,
the higher the corrosion.
5) Relief Valves
Does the PV give the flow capacity required by law? For calculating the
flow rate, contact Fort Vale. Hydrogen Peroxide requires a venting system
special relief capacity more than most. Bursting disc is ‘in parellell’
. i.e. PV valve and a separate bursting disc are next to each other, as
opposed to ‘in series’. i.e. where the PV valve has the bursting
disc below it.
6) Design temperature
Some products need to be transported at temperatures higher than than
120°C, therefore a special tank with thicker steel is required.
7) Electrics – for heating or cooling.
Where products have to be maintained within a specified temperature range,
then an electrical unit is required, whether its for keeping a chemical
at 45°C or beer at 1°C. We use Mannings units for heating, and
Klinge units for cooling.
8) Insulation
Rather than going to the expense of electrics, it might be more viable
to increase the insulation to 100mm, or in some cases 200mm. This allows
for the product temperature to remain more constant. Increasing the insulation
will reduce the size of the tank, otherwise there is a danger of being
outside ISO.
Reflective Sunshields. These can be added to the tank, to enhance the
insulation properties.
9) Swap Body’s
Their dimensions are outside ISO. They are generally higher, wider, and
of course longer than the ‘standard tank’. Typical dimensions
are:
Click
here for dimension table
They have additional corner castings to the standard ISO container, however
they retain corner castings at ISO so that they can be treated / handled
by the same equipment.
10) IMO 5 Gas Tanks
Gas tanks are generally made of mild steel, as opposed to stainless steel,
as the tare weight is generally a constraint. Mild is also cheaper than
stainless.
Routine shotblasting of the interior maybe required from time to time
to remove build up of scaling and or rust, due to oxidisation.
See section on Gas Tanks for
further details.
|
|